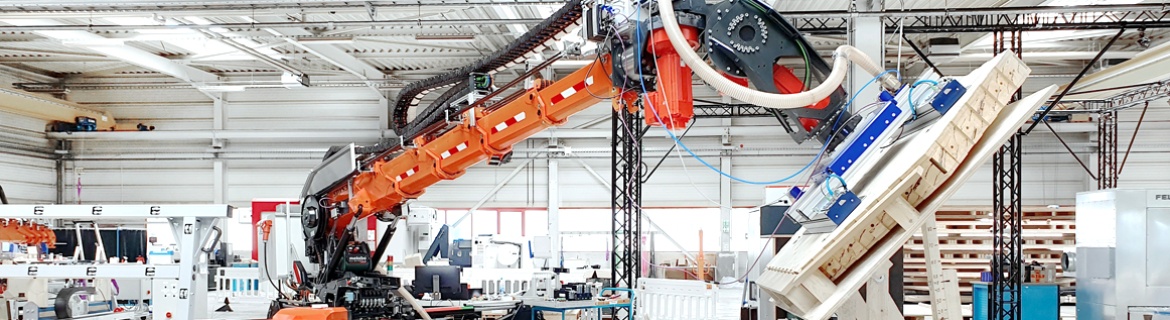
Instrumentation Platform for On-Site Large-Scale Robotic Construction
The main objective of this platform is twofold. On the one hand, the intention is to address the integration challenge of the Cluster's Research Network 1 (Multi-storey Building Systems) by developing methods and processes for cyber-physical on-site construction and element assembly of multi-storey buildings. The base platform for this investigation is a tower crane, which, as a handling system serving a large workspace, realises automated pick-up and place processes for prefabricated elements using novel handling and gripping concepts. To suppress sway motions and enable an autonomous transport and positioning of elements, the research conducted in RP 8-2 focuses on anti-sway control and trajectory generation methods in static and dynamic environments. To derive an environmental model and to monitor the construction site including dynamic obstacles, the tower crane is equipped with an image-based sensor network. The environmental model and a robotic total station network enable accurate positioning of elements in georeferenced coordinates.
On the other hand, the second objective is to address the performance challenge of the second research network by developing a robotic system for on-site construction with advanced haptic perception. A spyder crane is used to to automatically place elements in the assembly process of timber and long-span buildings with high positioning accuracy and utmost care to ensure the intactness of fragile elements. The high-positional accuracy is achieved by feedback control algorithms using absolute position feedback from a robotic total station network. The issues investigated in Research Project 16-2 range from smart teleoperation to fully autonomous control, including haptic feedback, automation of time-consuming tasks, force control, trajectory generation in contact situations, and machine-machine collaboration.